Entanglement of the fibre
- Threads Traces
- Oct 27, 2021
- 2 min read
Updated: Nov 15, 2021
Following the accidents, exploring the accidental qualities.
Accident. That’s what it takes to start a process. In a very simple act as trying to wash the wool to remove all dirt and smell - we found an alternative way. We took a piece of fleece, hot water, detergent (soap) and we used pressure and rolling motions. As we are used to do while washing the fabric. But an unexpected thing occured the fleece completely changed it’s structure. We created the first wet entanglement of the fibres of our own.
“Do we have to destroy the entanglement of the fibre to use it? Can’t we use it as an advantage and try to even mulitply enhence it rather than start all over?”
The fibres while growing create a specific structure. In traditional wool processing operation the strucutre has to be disentangled first, divided, to refer and be spun into a threat. But do we have to destroy the entanglement to use it? Can’t we use it as an advantage and try to even mulitply enhence it rather than start all over?
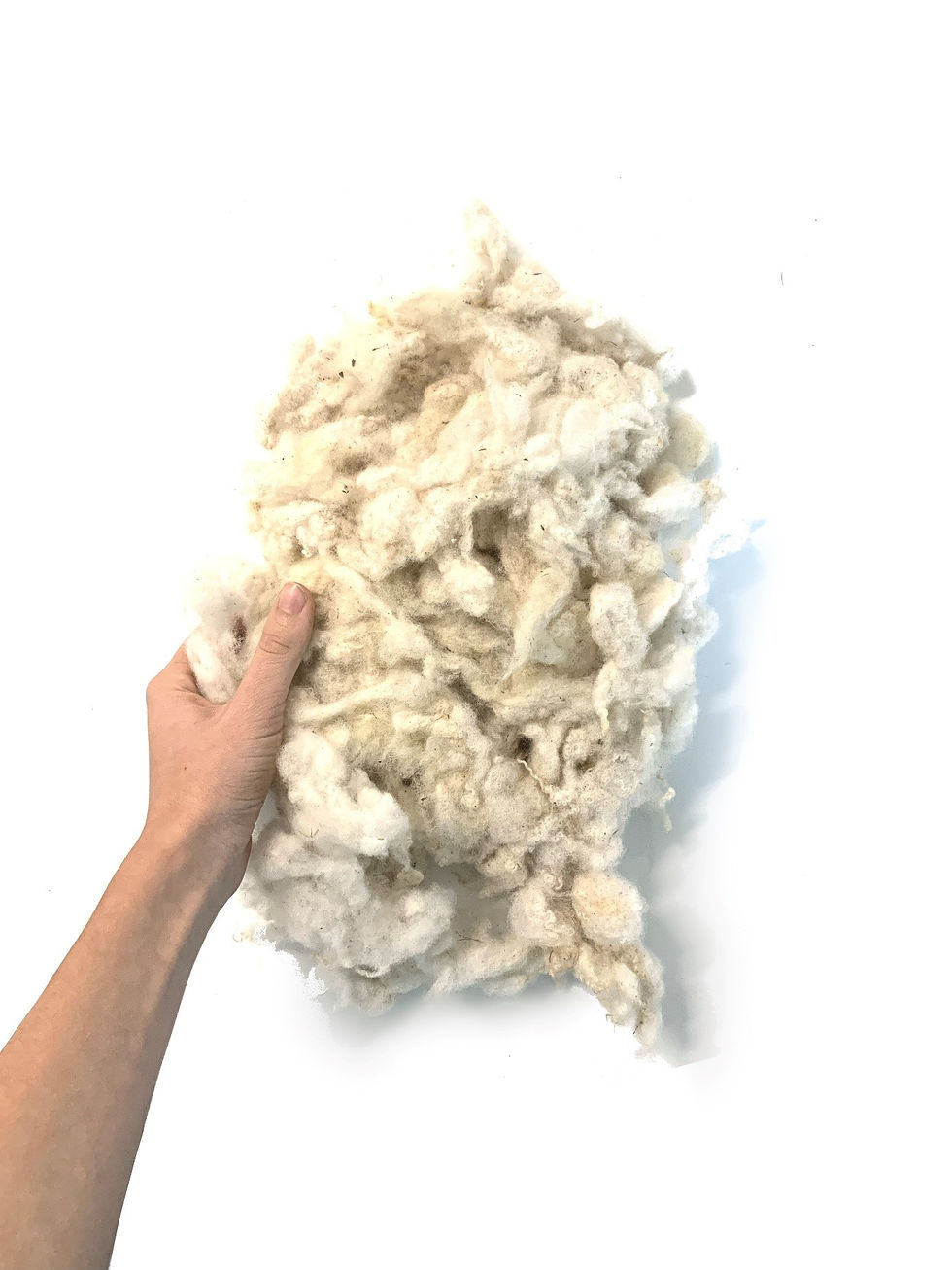
Image 1: First accidental felt. The strenght and structure were new and exciting but we needed to work further with shape.
Felt
Felt was our answer. By felt we mean a mass of wool which is entangled and dense enough to hold a shape and show some qualities (via second article). To create it we used two different techniques:
First - dry felting. A very impressive process to entangle wool with a special carved needle. The needle takes few fibres and pushes them deep into another ones to create a strong bond. It leads within the structure. Any possible shape can be achieved but in just a limited scale as both the tool and the basic building material – the fibre - are very small and it takes hours to handfelt just a little piece. The felt is firmed in locally but very effectively.
Second – wet felting. Process that enabled us to make a big pieces of ‚felt fabric‘. We got inspired by multiple old traditions like Mongolian and Iranian. And by laying a numerous layers of just a slightly loosen wool, pouring it with hot water with detergent to erect a keratin scales on individual fibres and than pushing, pulling, rolling and stepping on the piece to make the felt as entangled as possible. The outcome was very dense, strong and opposite to a dry felt very homogenous.

Image 2: The basic quality differences between dry and wet felt.
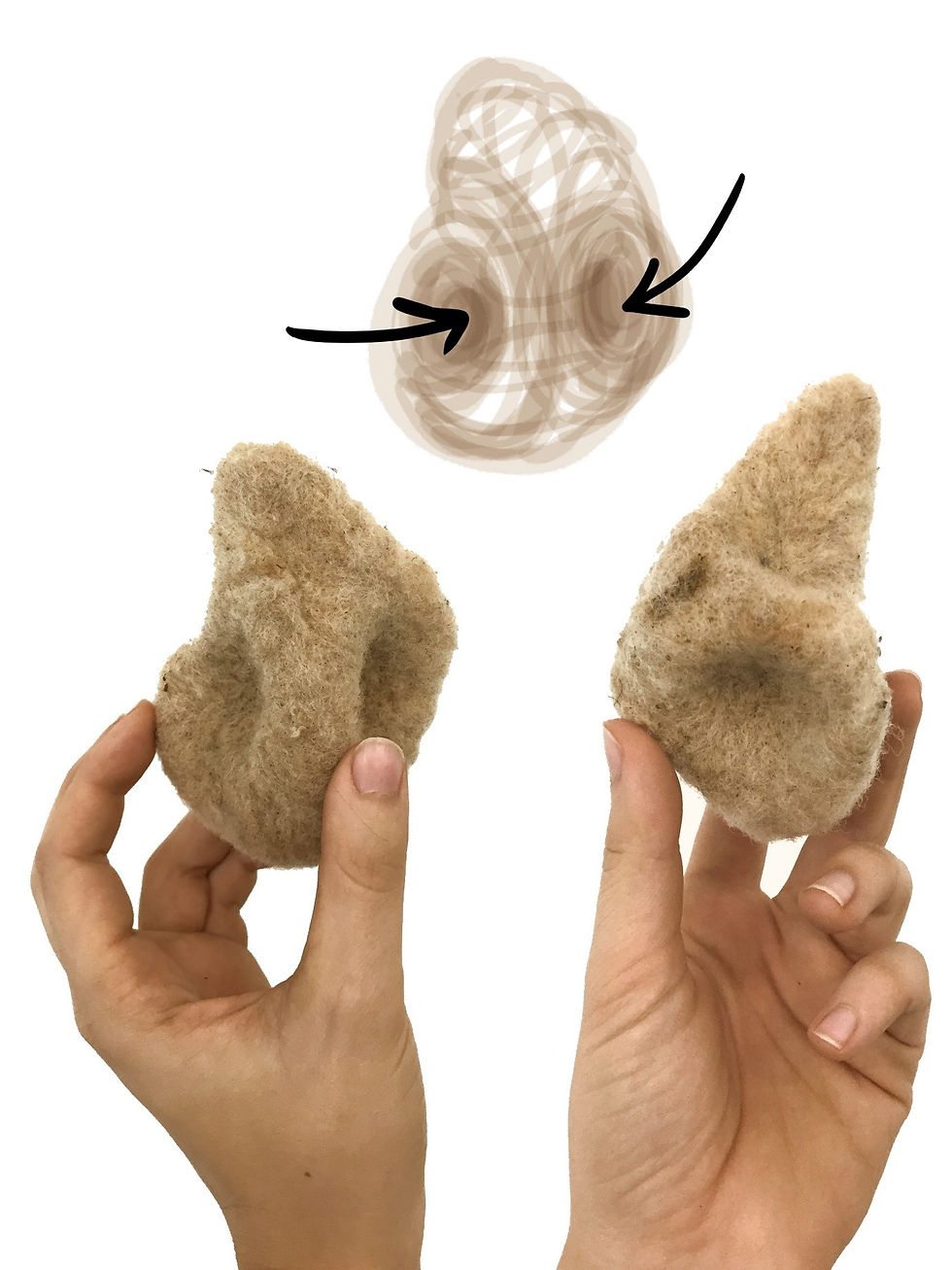
Image 3: Using an option of specific shape and different densities that dry felt offers.
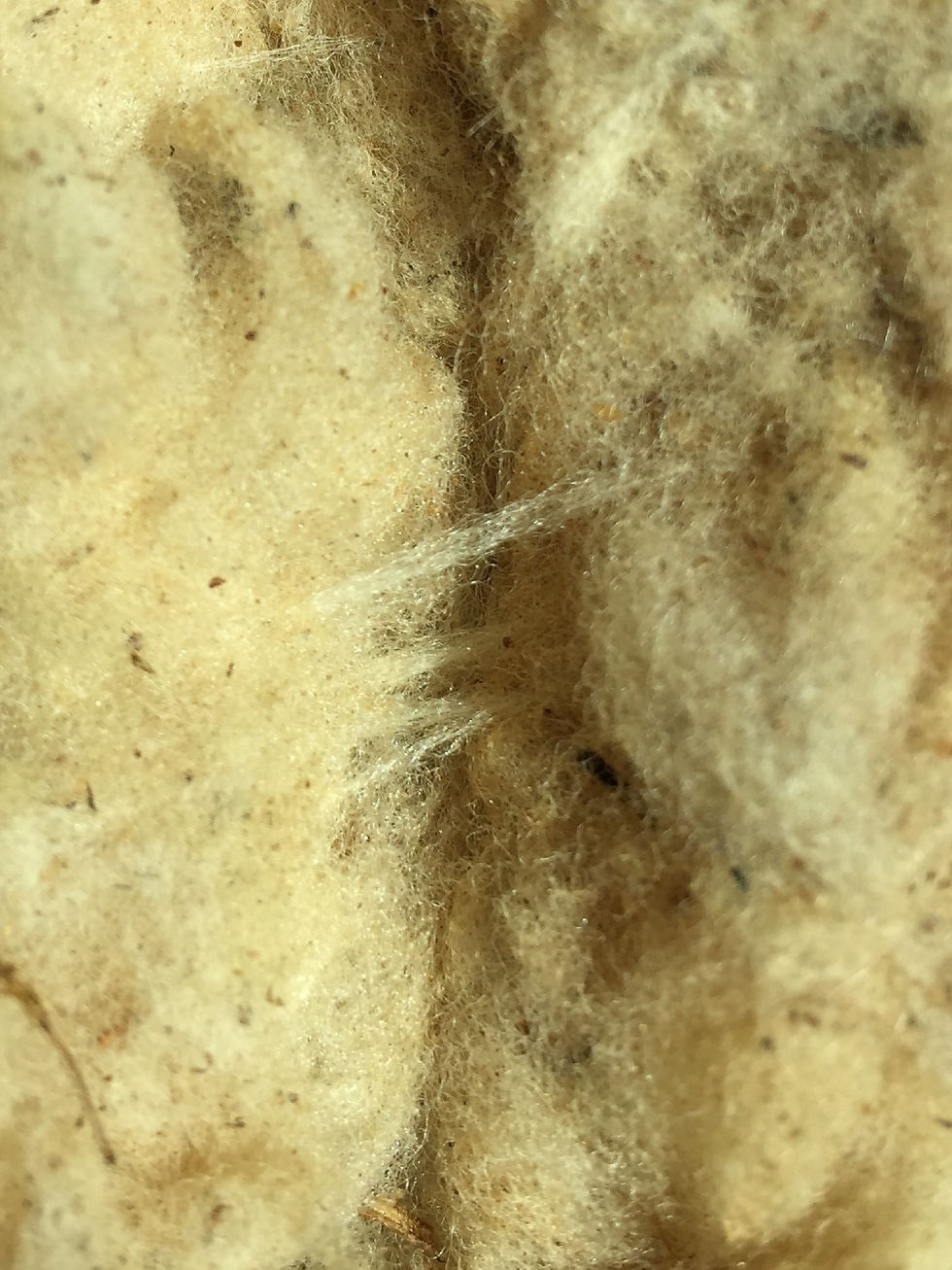
Image 4: Traces leading deep inside of dry-felted piece.

Image 5: Making of one of the first wet-felts usinig layered wool, hot water, detergent, plastic wrap, soft mat, plastic net and a lot of pressure.
Authors: Klarisa Ach-Hübner, Diana Bevelaquová. Midterm reviews (5.11.2021), FABUT WS 21/22
Comments