Carding
Carding is a mechanical process that disentangles, cleans, and intermixes fibers to produce a continuous web or sliver suitable for following procedures. This is achieved by passing the fibers between differentially moving surfaces covered by card clothing. The washed wool is sent through the devices to divide it into more parts. The clumps of wool are disentangled and shorter fibres are removed. Longer fibers are inter-mix to form a homogenous blend and they are aligned to form a net. Some smaller tangled impurities are also removed in the process.
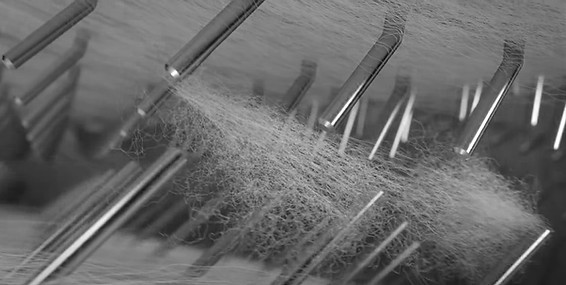
Preparation of Wool
To prepare the blended, conditioned loose scoured wool for carding, an exact amount of synthetic lubricant and water is mixed and applied to it. The usage of the lubricant is crucial to reduce fibre to metal friction and usage of water reduces the formation of static. If either occurs during the carding process it will lead to excessive fibre breakages and reduce processing efficiency.
The scoured wool still has some grease remaining, usually it is about 0.3% to 0.5% by weight, which is positive because wool grease in itself is a good processing lubricant.
In woolen processes is applied significantly larger amount of synthetic processing lubricant in comparison to worsted processes. This can range between 4% and 10% depending upon the actual components of the wool blend.
The purpose of adding higher quantities of processing lubricant is to reduce wastage by minimising the number of short fibres which fall out during the carding process and accumulate under the machine.

Woolen or Worsted
The process of carding is determined by the length of fibers as well as the final products we wish to make. The quality and length of wool depending on the breed of the sheep and the quality of living conditions.
The longer fibers are usually used for softer, finer yarns. They are sent through the following worsted processes. The final result can be a textile much softer and finer, f.e. suits, activewear, etc...
The shorter, much more tangled fibers are used for woolen processes, for garments with visible texture, such as overcoats, tweed, felted textiles, etc...

Machine Carding
Large companies which are making woolen garments or textiles today are using more efficient carding machines (called cards). Those allow us to form webs with fibers perfectly aligned and ready for other procedures.
These cards do not store fiber in the card cloth as it is made in hand carding, rather, fiber passes through the workings of the carder for storage or for additional processing by other machines.
​
If the wool we sent through the carding machine consist of shorter fibers, in the end, the final web is divided into slubbings. These are further used for woolen processes. They are ready to be spun into a thicker yarn with a rough texture.
If we worked with wool, which consists of longer fibers the final web is formed into a sliver. This result is sent to worsted processes (gilling, drawing, spinning) to form a finer, thinner yarn.
​
The process of machine carding is more efficient in the production of waste. In woolen processes, the shorter fibers are lubricated before the process of carding. It prevents them from falling out during the carding process. In worsted processes, the wastage of shorter fibers comes with combing. It is possible to use the waste short fibers from worsted carding (combing) back in woolen processes or felted textiles.
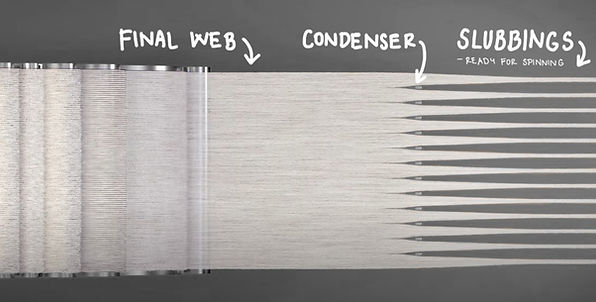.jpg)


The Mechanics of Card
A typical card has a single large drum (the swift) accompanied by a pair of in-feed rollers (nippers), one or more pairs of worker and stripper rollers, a fancy, and a doffer. In-feed to the carder is usually accomplished by hand or by conveyor belt and often the output of the cottage carder is stored as a batt or further processed into roving and wound into bumps with an accessory bump winder. The cottage carder in the image below supports both outputs.
​
Raw fiber, placed on the in-feed table or conveyor is moved to the nippers which restrain and meter the fiber onto the swift. As they are transferred to the swift, many of the fibers are straightened and laid into the swift‘s card cloth. These fibers will be carried past the worker/stripper rollers to the fancy.
As the swift carries the fibers forward, from the nippers, those fibers that are not yet straightened are picked up by a worker and carried over the top to its paired stripper. Relative to the surface speed of the swift, the worker turns quite slowly. This has the effect of reversing the fiber. The stripper, which turns at a higher speed than the worker, pulls fibres from the worker and passes them to the swift. The stripper‘s relative surface speed is slower than the swift‘s so the swift pulls the fibers from the stripper for additional straightening.
Straightened fibers are carried by the swift to the fancy. The fancy‘s card cloth is designed to engage with the swift‘s card cloth so that the fibers are lifted to the tips of the swift‘s card cloth and carried by the swift to the doffer. The fancy and the swift are the only rollers in the carding process that actually touch.
The slowly turning doffer removes the fibers from the swift and carries them to the fly comb where they are stripped from the doffer. A fine web of more or less parallel fibre, a few fibres thick and as wide as the carder‘s rollers, exits the carder at the fly comb by gravity or other mechanical means for storage or further processing.

Hand Carding
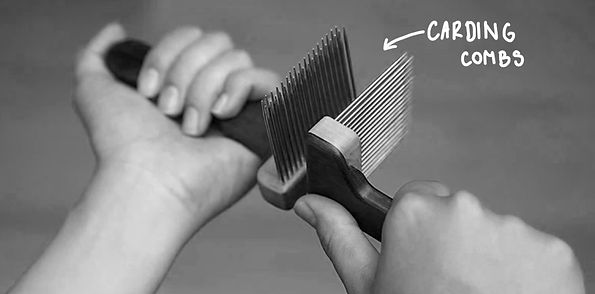
The process of hand carding the wool is determined by the length of the fibers as well as by the final purpose and wanted the appearance of the textile or garment. We divide it into two categories - worsted and woolen. Hand carding is an activity normally done outside or over a drop cloth, depending on the wool‘s cleanliness.
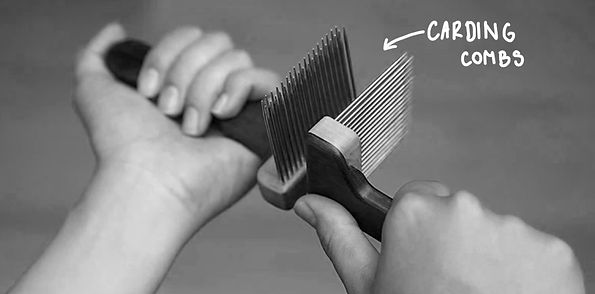
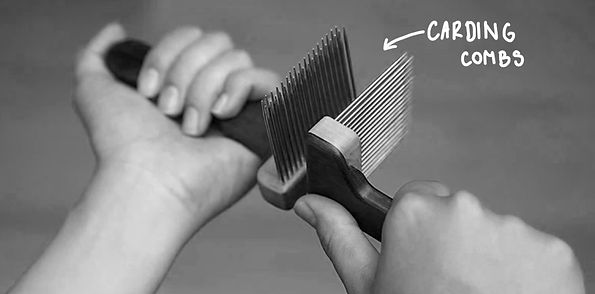
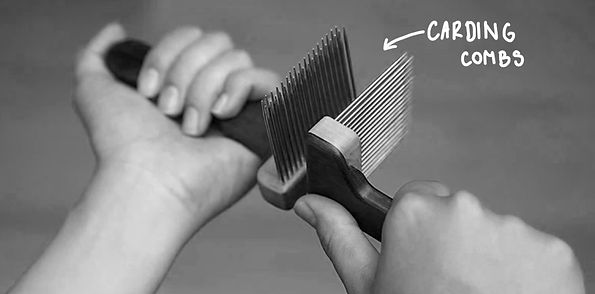
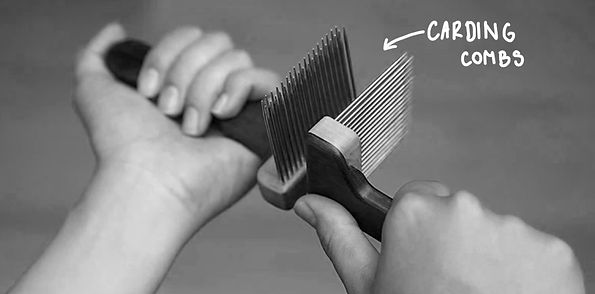


Drum Carding
The drum carder was invented for more efficient carding of long as well as short fibres. It is possible to blend different colours or types of fibres on it and form a rolag or a strand. The principle of drum carder created a basis for contemporary carding machines. Two rollers covered in card clothing are turning in opposite directions, opening up and disentangling the woollen fibres. The washed wool comes from one end then it is sent through the rollers and holt on the bigger cylinder by pins. The knitting needle is used for taking the carded wool off. The final result of drum carding is a rolag or a web.
